Basic Info.
Product Description
Blind Flanges
Blind flanges have the face thickness of a flange, a matching face type, and similar bolting pattern.
Material: Carbon, Alloy and Stainless Steel
Standards: ASTM A105, ASTM A182
Sizes: 1/2'' to 24'', Customized up to 48''
Thickness: Schedule 10(S) to SCH 160
Pressure Ratings: Class 150 to 2500
Face Type: RF, RTJ
Blind flange is like a flange cover, also called blind disk or flanged pipe plug. Blind flange has no holes in the centre, for to seal the pipe opening. So it's function is the same as the pipe plug or the pipe cap. The difference is blind flange is a detachable equipment, easy to replace or do maintenance.
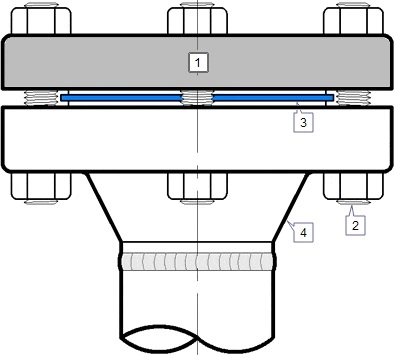
1. Blind flange 2. Stud Bolt 3. Gasket 4. Other flange
Major Function - Where to use
The blind flange is used to close ends of piping systems. It is a kind of round plate with no center hold but with all the proper bolt holes. This blind flange is available in various sizes and materials and is used to provide positive closer on the ends of pipes, valves or equipment nozzles. This flange helps in easy access to a line once it has been sealed. The blind flange is sometimes custom made or machined to accept a nominal sized pipe to which reduction is being made.
A blind flange is useful for making repairs to a pipeline further up the line. In fact, during construction of a pipeline, a blind flange may be built into the final length of pipe. This allows for expansion or continuation of the pipeline simply by adding onto the final flange.
Manufacturing Types and Costs
Generally has four types: Forging, casting and forging, medium plate cutting, casting, the price of forging products is the highest, the middle plate is the second, casting and forging is the lowest and casting is the worst process when compared with others.
The best quality is forging and medium plate, casting and forging is a bit worse.
Casting Blind Flange
The shape of the the casting flange blank is accurate, has the small processing capacity, the cost is low, but there are casting defects (air hole crack inclusions); And the streamline of the internal casting part is bad (if it is a cutting part, the streamline is worse).
Forging Blind Flange
Forged blind flange generally have lower carbon content than cast flanges and are not easily to rust. Forgings have better streamlined shape, denser structure and better mechanical properties than cast flanges;
If the forging process is improper, the grain will be large or uneven, and the hardening crack will occur. The forging cost is higher than the casting flange.
Forgings can withstand higher shear and tensile forces than castings.
Advantage of blind flanges
- A much more cost efficient way to seal a pipe when doing repairs.
- Blind flanges are convenient to install.
- They can save a good amount of time and money.
Features of blind flanges
Some important features of blind flanges are as follows:
- Blind flanges are sometimes supplied with NPT fittings which allow pressure test connections to be fitted.
- They are used to blank off the ends of pipe.
- They are also used to blank off the ends of valves and pressure vessel opening.
- Considering factors like internal pressure and bolt loading, blind flanges, especially in the larger sizes, are the most highly stressed of all types of flanges.
- Since the maximum stresses in a blind flange are bending stresses at the center, they can safely be allowed to be higher than in other types of flanges.
- Blind flanges are made to fit standard pipes in all sizes.
Materials
Pipe flanges are manufactured in all the different materials like stainless steel, cast iron, aluminium, brass, bronze, plastic etc. but the most used material is forged carbon steel and have machined surfaces.
Flanges are welded to pipe and equipment nozzle. Accordingly, it is manufactured from the following materials;
- Carbon steel
- Low alloy steel
- Stainless steel
- Combination of Exotic materials (Stub) and other backing materials
The list of materials used in manufacturing is covered in ASME B16.5 & B16.47.
- ASME B16.5 -Pipe Flanges and Flanged Fittings NPS ½" to 24"
- ASME B16.47 -Large Diameter Steel Flanges NPS 26" to 60"
Commonly used Forged material grads are
- Carbon Steel: - ASTM A105, ASTM A350 LF1/2, ASTM A181
- Alloy Steel: - ASTM A182F1 /F2 /F5 /F7 /F9 /F11 /F12 /F22
- Stainless Steel: - ASTM A182F6 /F304 /F304L /F316 /F316L/ F321/F347/F348
Frequently used astm grades
Material | Fittings | Flanges | Valves | Bolts & Nuts |
Carbon Steel | A234 Gr WPA | A105 | A216 Gr WCB | A193 Gr B7 A194 Gr 2H |
A234 Gr WPB | A105 | A216 Gr WCB | ||
A234 Gr WPC | A105 | A216 Gr WCB | ||
Carbon Steel Alloy High-Temp | A234 Gr WP1 | A182 Gr F1 | A217 Gr WC1 | A193 Gr B7 A194 Gr 2H |
A234 Gr WP11 | A182 Gr F11 | A217 Gr WC6 | ||
A234 Gr WP12 | A182 Gr F12 | A217 Gr WC6 | ||
A234 Gr WP22 | A182 Gr F22 | A217 Gr WC9 | ||
A234 Gr WP5 | A182 Gr F5 | A217 Gr C5 | ||
A234 Gr WP9 | A182 Gr F9 | A217 Gr C12 | ||
Carbon Steel Alloy Low-Temp | A420 Gr WPL6 | A350 Gr LF2 | A352 Gr LCB | A320 Gr L7 A194 Gr 7 |
A420 Gr WPL3 | A350 Gr LF3 | A352 Gr LC3 | ||
Austenitic Stainless Steel | A403 Gr WP304 | A182 Gr F304 | A182 Gr F304 | A193 Gr B8 A194 Gr 8 |
A403 Gr WP316 | A182 Gr F316 | A182 Gr F316 | ||
A403 Gr WP321 | A182 Gr F321 | A182 Gr F321 | ||
A403 Gr WP347 | A182 Gr F347 | A182 Gr F347 |
ASTM standards define the specific manufacturing process of the material and determine the exact chemical composition of pipes, fittings and flanges, through percentages of the permitted quantities of carbon, magnesium, nickel, etc., and are indicated by "Grade".
The usual materials of flanges include stainless steel, carbon steel, aluminum and plastic. The choice of the material largely depends on the purpose of the flange. For example, stainless steel is more durable and is necessary for heavy use. On the other hand, plastic is more feasible for use in the home because of its reasonable price and easy installation. The materials used for flanges are under the designation of the American Society of Mechanical Engineers.
Flange materials acc. to ASTM
The most common materials for pipe flanges (forged grades) are: ASTM A105 (carbon steel high temperature to match A53/A106/API 5L pipes), A350 Grades LF1/2/3 (carbon steel low temperature to match A333 pipes), A694 Grades F42 to F80 (high yield carbon steel to match API 5L pipe grades), ASTM A182 Grades F5 to F91 (alloy steel flanges to match A335 pipes), A182 Grade F304/316 (stainless steel flanges to match A312 SS pipes), A182 Gr. F44/F51/F53/F55 (duplex and super duplex to match A790/A928 pipes) and various nickel alloy grades (Inconel, Incoloy, Hastelloy, Monel).
The material qualities for these flanges are defined in the ASTM standards.
What are ASTM Grades?
For example, a carbon steel pipe can be identified with Grade A or B, a stainless-steel pipe with Grade TP304 or Grade TP321, a carbon steel fitting with Grade WPB etc.
Standard
Pipe Flange Standards mainly include three systems in the world, ANSI/ASME flange system(American), DIN flange system(European system), JIS flange system, other system made according to this three systems, like GB flange standard, which mainly made according to ANSI/ASME and DIN flange standard, Duwa Piping supplies those flanges with top quality and soonest delivery time.
ASME standards
- ASME B16.1 - Gray Iron Pipe Flanges and Flanged Fittings: Classes 25, 125, and 250
- ASME B16.5 - Pipe Flanges and Flanged Fittings: NPS 1/2 through NPS 24 Metric/Inch Standard
- ASME B16.20 - Ring Joint Gaskets and Grooves for Steel Pipe Flanges
- ASME B16.21 - Nonmetallic Flat Gaskets for Pipe Flanges
- ASME B16.24 - Cast Copper Alloy Pipe Flanges and Flanged Fittings: Classes 150, 300, 600, 900, 1500, and 2500
- ASME B16.34 - Large Diameter Steel Flanges (NPS 26 through NPS 60)
- ASME B16.36 - Orifice Flanges
- ASME B16.42 - Ductile Iron Pipe Flanges and Flanged Fittings: Classes 150 and 300
- ASME B16.47 - Large Diameter Steel Flanges (NPS 26 Through NPS 60)
ASTM standards
- ASTM A105 - Specification for Carbon Steel Forgings for Piping Applications
- ASTM A182 - Specification for Forged or Rolled Alloy Steel Pipe Flanges, Forged Fittings, and Valves and Parts for High Temperature Service
- ASTM A193 - Specification for Alloy Steel and Stainless Steel Bolting Materials for High Temperature Service
- ASTM A194 - Specification for Carbon and Alloy Steel Nuts for Bolts for High Pressure and High Temperature Service
- ASTM A694 - Specification for Carbon and Alloy Steel Forgings for Pipe Flanges, Fittings, Valves, and Parts for High-Pressure Transmission Service
- ASTM A707 - Specification for Flanges, Forged, Carbon and Allow Steel for Low Temperature Service
AWWA standards
- AWWA C115 - Standard for Flanged Ductile Iron Pipe with Ductile-Iron or Gray-Iron Threaded Flanges
ISO standards
- ISO 5251 - Stainless steel butt-welding fittings
MSS standards
- MSS SP-6 - Standard Finishes for Contact Faces Pipe Flanges and Connecting End Flanges of Valves and Fittings
- MSS SP-9 - Spot Facing for Bronze, Iron and Steel Flanges
- MSS SP-25 - Standard Marking Systems for Valves, Fittings, Flanges, and Unions
- MSS SP-44 - Steel Pipeline Flanges
- MSS SP-53 - Quality Standards for Steel Castings and Forgings for Valves, Flanges and Fittings and Other Piping Components - Magnetic Particle
- MSS SP-54 - Quality Standards for Steel Castings and for Valves, Flanges and Fittings and Other Piping Components - Radiographic
- MSS SP-55 - Quality Standards for Steel Castings and for Valves, Flanges and Fittings and Other Piping Components - Visual
- MSS SP-75 - High Test Wrought Butt Welding Fittings
- MSS SP-106 - Cast Copper Alloy Flanges and Flanged Fittings Class 125,150, and 300
- ASME B16.5 and ASME B16.47 cover pipe flanges up to NPS 60 (B16.5 from 1/2″ to 24″ and B16.47 from 26″ to 60″). ANSI
- B16.47 covers two series of flanges, Series A is equal to MSS SP-44-44, and Series B is equal to API 605 (API 605 has been canclled).
FAQs
The most frequently asked questions regarding flanges and flange fittings have to do with how flanges fit on specific steel tube and steel pipe ends.
How flanges operate?
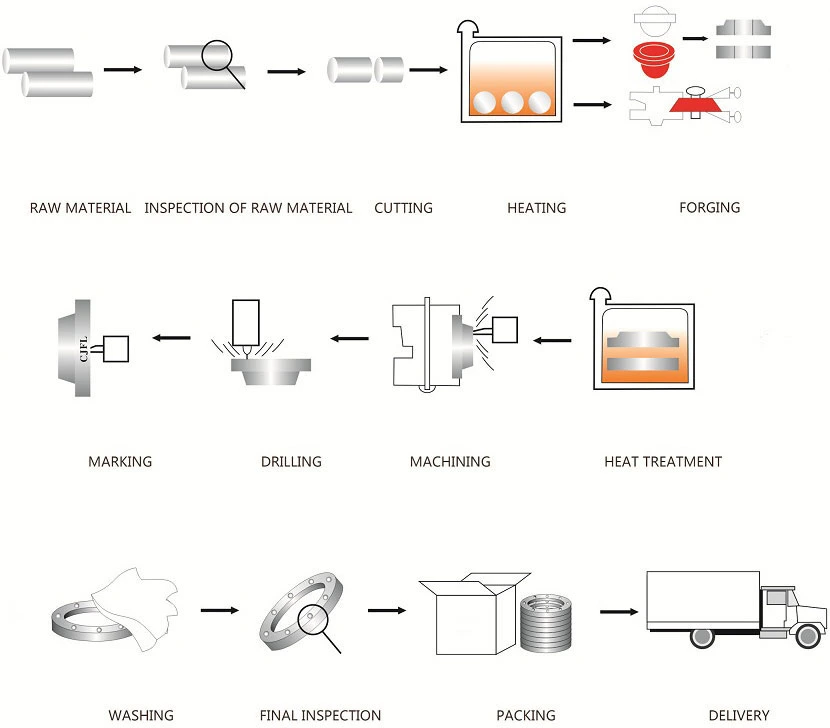
Flanges have flat or flush surfaces that are vertical to the pipe to which they are attached. The attachment process involves mechanically joining two or more faces using bolts, adhesives, collars, or welds. Due to the attachment requirements, a flange must fit the equipment or pipe that it's designed. That's why it's necessary to check all the possible specifications and dimensions to ascertain that it's of the right size, type, and material.
Flange material standards
Flanges are used to connect pipes or other equipment components in various industries, and they come in a variety of materials and sizes. Flange material standards are developed by standard-setting organizations and describe the properties and characteristics of different materials that can be used to make flanges. Some examples of commonly used flange material standards include:
- ASTM A105: This standard covers forged carbon steel piping components, including flanges, that are suitable for use in high-pressure applications.
- ASTM A182: This standard covers forged or rolled alloy steel pipe flanges, forged fittings, and valves and parts intended for high-temperature service.
- ANSI B16.5: This standard specifies the dimensions, tolerances, and markings for steel pipe flanges and flanged fittings.
- DIN 2632-2638: This standard defines the dimensions and tolerances for flanges made from steel, including carbon steel, stainless steel, and other alloys.
- ASME B16.47: This standard covers large diameter steel flanges, typically used in high-pressure applications where larger bore sizes are needed.
- BS 4504: This British standard covers circular flanges for pipes, valves, and fittings, with nominal sizes ranging from 15 to 600 mm.
The choice of flange material standard will depend on various factors such as the application, the environment, the fluid being transported, and the required performance characteristics. For example, high-pressure applications may require flanges made from materials with high strength and durability, while corrosive environments may require flanges made from materials with good resistance to corrosion.
Flange Inspection
Before dispatching from manufacture each flange is inspected to ensure quality. During an inspection you have to check the following;
- Outer & Inner Diameter of body
- Bolt Circle & Bolt hole Diameter
- Hub Diameter & thickness of weld end
- Length of the Hub
- Straightness and alignment of the bolt hole
ASME B16.5 and B16.47 standards cover permissible tolerances for inspection.
ASME B16.5 and B16.47 standards cover permissible tolerances for inspection.
Packing
Because of the normal wooden boxes or wooden pallets have to do fumigation treatment, we usually use plywood pallet or plywood case or box to pack steel flanges without fumigation treatment.
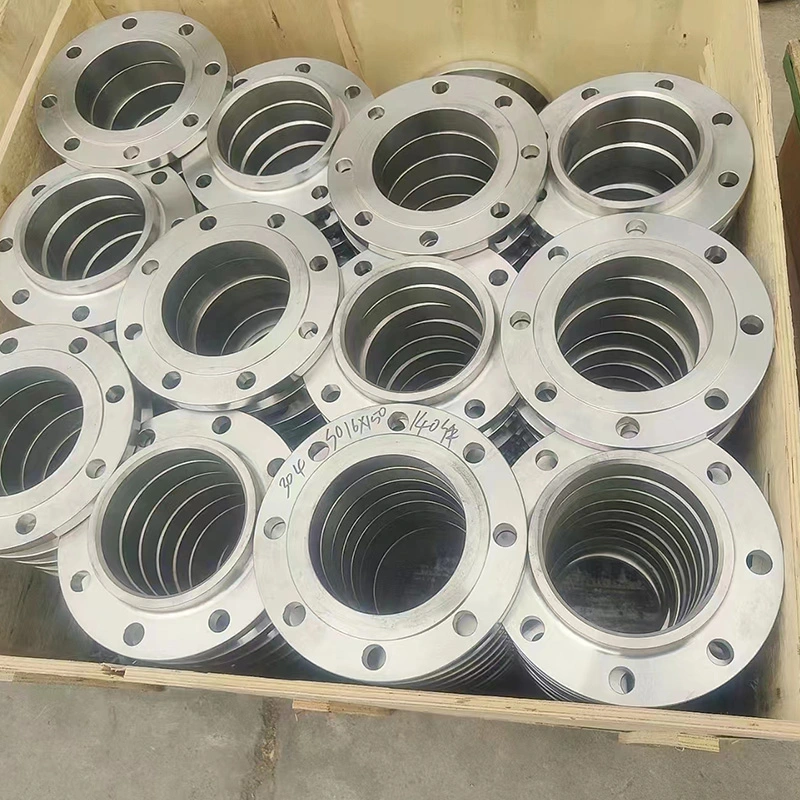
Flanges Applications
A flange is a method of connecting pipes, valves, pumps, and other equipment to form a piping system. It also provides easy access for cleaning, inspection, or modification.
When a piping joint requires to be dismantled, flanges are being used. These are primarily used on equipment, valves, and specialty items. Breakout flanges are provided at predetermined intervals in certain pipelines where maintenance is a regular occurrence. The flanges, gaskets, and bolting make up a flanged joint, which is made up of three separate but interconnected components. To achieve a leak-proof joint, special controls are required in the selection and application of all of these elements.
Here are the details of Flanges about their advantages and their applications.